Discover Build Masters Projects, your trusted partner in sustainable construction and expert project management.
Building and Construction Jargon: A Guide for New Home Builders
Understand the key terms and concepts in building and construction with our comprehensive guide tailored for new home builders. From architectural terms to sustainability practices, get the insights you need to navigate your building project confidently.
George Eleter
6/8/20247 min read
If you are considering starting a building project, you need to understand the language. Here is a detailed list of industry-specific jargon, terms, and concepts that are commonly used in building and construction projects, tailored for new home builders:
1. Architectural Terms
Blueprints: Detailed technical drawings of a building project.
Blueprints serve as a guide for builders, showing the dimensions, construction methods, and materials needed.
These documents are essential for ensuring everyone involved in the construction process is on the same page.
Elevation: A drawing that shows the exterior view of a building from one side.
Elevations provide a visual representation of how the finished structure will appear.
They convey the architectural style, materials, and other key features of the building's exterior.
Footprint: The area on a building site that is occupied by the structure.
The footprint determines the space required for the foundation and can impact zoning and building codes.
Understanding the footprint is crucial for site planning and environmental impact assessments.
Floor Plan: A scale diagram of the arrangement of rooms in one story of a building.
Floor plans show how spaces within a building are organized, including room sizes, wall placements, and door/window locations.
These diagrams help visualize traffic flow and functionality within the space.
2. Construction Phases
Pre-construction: This is the planning phase before the actual building begins. Key activities include:
Design: Creating detailed architectural and engineering plans.
Permits: Securing necessary legal permissions from local authorities.
Budgeting: Estimating costs for labour, materials, and other expenses to ensure financial feasibility.
Groundbreaking: A ceremonial event to mark the official start of construction work on the site. Often involves key stakeholders and signifies the transition from planning to action.
Framing: The process of constructing the skeletal structure of a building. This includes:
Wall Frames: Building vertical supports for walls.
Roof Trusses: Assembling triangular units that support the roof.
Floor Joists: Horizontal supports that form the building’s floors.
Dry-in: The stage when the building is weatherproofed with roofing and external walls but not yet finished inside. Essential steps include:
Roof Installation: Adding shingles or other roofing materials.
Exterior Walls: Installing siding, brick, or other exterior wall coverings.
Windows and Doors: Fitting in window panes and door frames to seal the structure against weather elements.
Punch List: A comprehensive list detailing final tasks or repairs needed to complete the project. This can include:
Minor Repairs: Fixing any defects or issues discovered during final inspections.
Final Touches: Completing paint jobs, installing fixtures, and ensuring all systems (plumbing, electrical) are operational.
3. Materials
Aggregate: Materials like sand, gravel, or crushed stone used in concrete. Aggregates provide volume, stability, and resistance to wear or erosion within the concrete mix, enhancing its structural integrity. They are categorized into fine aggregates (like sand) and coarse aggregates (such as gravel).
Rebar (Reinforcing Bar): Steel bars are used to reinforce concrete structures. Rebars significantly improve the tensile strength of concrete, which is otherwise weak in tension but strong in compression. They come in various sizes and grades, each suited for different types of construction projects.
OSB (Oriented Strand Board): An engineered wood product similar to plywood made from compressed wood strands. OSB is widely used for sheathing in walls, flooring, and roof decking due to its high strength-to-weight ratio and cost-effectiveness compared to traditional plywood.
Drywall: Panels made from gypsum plaster pressed between two thick sheets of paper, used for interior walls and ceilings. Drywall is valued for its ease of installation and finishing, fire resistance properties, and ability to create smooth surfaces suitable for painting or wallpapering.
4. Structural Elements
Beam: A horizontal structural element that supports loads. Beams are crucial in construction as they bear the weight of floors, roofs, and walls, distributing these loads to the columns or foundations. They come in various shapes and materials, such as steel, concrete, and wood, each chosen based on the specific requirements of the structure.
Column: A vertical structural element that transfers loads from above to below. Columns are fundamental in supporting beams and slabs, ensuring the stability of a building. They can be made from reinforced concrete, steel, or timber. Columns must be designed to withstand compressive forces, preventing buckling under heavy loads.
Truss: A framework typically consisting of rafters, posts, and struts supporting a roof or bridge. Trusses are engineered to provide maximum strength with minimal material by forming triangular units that distribute weight evenly. Common types include King Post Trusses, Queen Post Trusses, and Howe Trusses. Each type is suited for different spans and load conditions.
By understanding and correctly implementing these structural elements—beams for horizontal load distribution, columns for vertical load transfer, and trusses for efficient weight support—you can ensure the integrity and safety of any construction project.
5. Mechanical Systems
Mechanical systems are integral to the functionality and comfort of any building. They encompass various components that ensure proper climate control, water supply, and electrical distribution. Here are key elements within mechanical systems:
HVAC (Heating, Ventilation, and Air Conditioning):
Heating: Systems such as furnaces, boilers, and heat pumps that provide warmth during colder months. These can be powered by electricity, natural gas, or other fuels.
Ventilation: Mechanisms that circulate air within a building to maintain indoor air quality. This includes exhaust fans, air ducts, and filters designed to remove contaminants and provide fresh air.
Air Conditioning: Units that cool indoor spaces during warmer months. These systems often include components like compressors, condensers, and evaporators to regulate temperature and humidity.
Plumbing Rough-In:
The initial phase of plumbing installation where pipes are strategically laid out based on the building's design. This stage occurs before walls, floors, or ceilings are closed up.
It involves setting up water supply lines for potable water as well as drainage pipes for wastewater removal. Proper rough-in ensures the correct positioning of fixtures such as sinks, toilets, and showers once the building progresses to later stages.
Electrical Rough-In:
The process of installing electrical wiring and boxes within walls before drywall or other wall materials are applied.
This includes routing electrical cables through studs and joists to power outlets, switches, lighting fixtures, and appliances. Proper rough-in ensures that all electrical components are safely connected and accessible for the final installation phases.
By understanding these essential mechanical systems—HVAC for climate control, plumbing rough-in for water management, and electrical rough-in for power distribution—you can ensure a building is both functional and comfortable for its occupants.
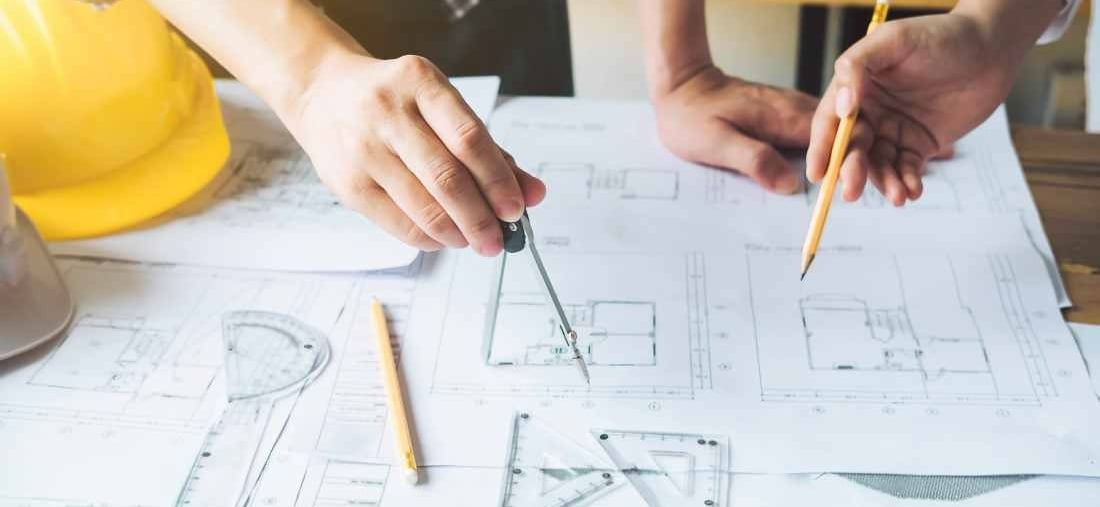
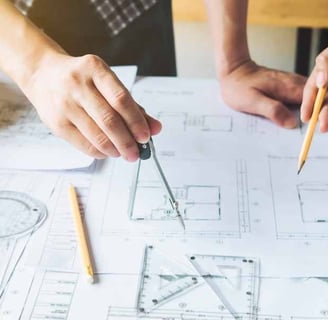

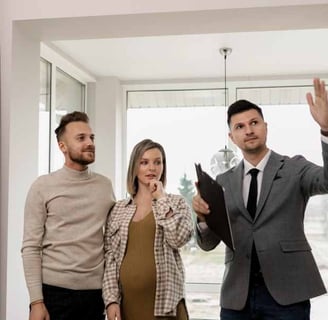
6. Building Codes and Permits
Zoning Laws:
Definition: Regulations determining how land can be used in different areas.
Purpose: Ensure that areas are used in a manner consistent with community plans, enhancing urban development and controlling density.
Examples: Residential, commercial, industrial, and agricultural zones.
Building Permit:
Definition: An official approval is required before construction can begin.
Purpose: Ensures the construction project complies with local building codes and safety regulations.
Process: Typically involves submitting detailed plans and project specifications to the local building department for review.
Occupancy Permit:
Definition: Certification that a building is safe for people to occupy.
Purpose: Confirms that all necessary inspections have been completed and the building meets all relevant codes and standards for occupancy.
Process: Issued after final inspection of the completed construction project, ensuring it is safe for use.
7. Sustainability Terms
LEED (Leadership in Energy and Environmental Design):
Definition: A globally recognized green building certification program.
Purpose: Promotes environmentally responsible, healthy, and resource-efficient building practices.
Certification Levels: Certified, Silver, Gold, and Platinum based on the number of points earned in various sustainability categories.
Key Areas: Sustainable sites, water efficiency, energy and atmosphere, materials and resources, indoor environmental quality.
Energy Star:
Definition: A program run by the U.S. Environmental Protection Agency (EPA) that certifies energy-efficient products and practices.
Purpose: Helps businesses and individuals save money while protecting the environment through superior energy efficiency.
Scope: Includes appliances, buildings, industrial facilities, and more.
Benefits: Reduces greenhouse gas emissions, lowers energy bills, and improves overall energy management.
Net Zero Energy Building:
Definition: A building that produces as much renewable energy as it consumes over the course of a year.
Features:
On-Site Renewable Energy Systems: Such as solar panels or wind turbines.
High-Efficiency Systems: Advanced HVAC systems, LED lighting, high-performance windows.
Energy Conservation Strategies: Enhanced insulation and airtight construction to minimize energy loss.
Benefits:
Environmental Impact: Significantly reduces carbon footprint.
Cost Savings: Lower operational costs due to reduced reliance on external energy sources.
Resilience: Greater energy independence and reliability.
8. Financial Terms
Estimate: An approximation of the cost to complete a project.
Purpose: Provides a preliminary financial overview to help with budgeting and decision-making.
Components: Includes material costs, labor, equipment, and contingency allowances.
Use Cases: Often used during the planning phase before finalizing a budget.
Bid: An offer by a contractor to complete work at a specified price.
Process: Contractors submit bids in response to a project's request for proposals (RFP).
Elements: Typically includes detailed cost breakdowns, timelines, and terms of service.
Evaluation: Clients review bids based on cost, experience, and proposed timelines before awarding the contract.
Change Order: An amendment to the original construction contract detailing changes in work scope or costs.
When Used: Issued when there are modifications to project plans that affect cost or schedule after the contract is signed.
Details: Specifies new terms, including additional costs, revised deadlines, and any impact on project deliverables.
Approval Process: Requires agreement from both parties—client and contractor—before implementation.
9. Concepts Related To Quality And Safety
QA/QC (Quality Assurance/Quality Control)Quality Assurance (QA): Involves systematic activities and procedures implemented within a quality system to ensure that quality requirements for a product or service will be fulfilled. QA focuses on preventing defects by improving processes.
Key Activities:
Process checklists
Project audits
Process standards
Benefits:
Enhances process efficiency
Reduces rework costs
Quality Control (QC): Entails the operational techniques and activities used to fulfill quality requirements. QC focuses on identifying defects in the actual products produced.
Key Activities:
Inspection and testing of materials and products
Monitoring and measuring performance
Corrective actions
Benefits:
Ensures final product meets specifications
Increases customer satisfaction
PPE (Personal Protective Equipment)
Refers to specialized clothing or equipment worn by employees for protection against health and safety hazards.
Types of PPE:
Helmets: Protects head from impact injuries.
Gloves: Shields hands from chemicals, cuts, and abrasions.
Goggles: Guards eyes against flying particles, chemical splashes, and harmful radiation.
Importance:
Minimizes risk of injury or illness in hazardous environments
Compliance with occupational safety regulations
Implementation:
Conduct hazard assessments to identify required PPE.
Provide training on proper use, care, and maintenance of PPE.
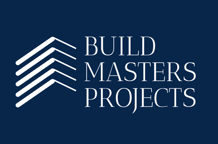
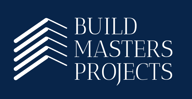
Building Maters Projects ©2024
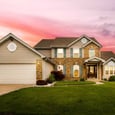
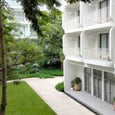
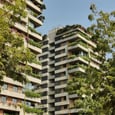
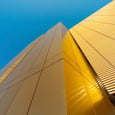
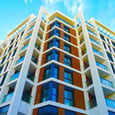
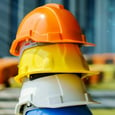
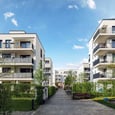
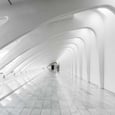
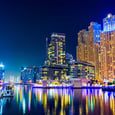
Subscribe to Industry News: